Overview
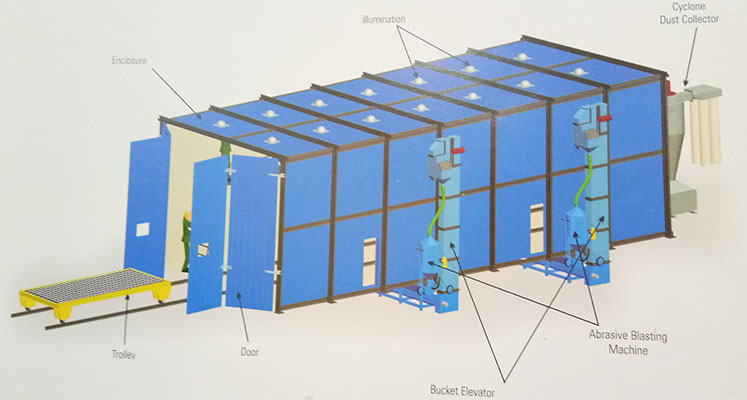
Essentially an efficient Blast Room System consists of:
- Encloser
- Abrasive Blasting Machine
- Dust Collector (Fabric/Pleated/Cartridge/Cyclone)
- Blasting Media Recovery & Separation System
- Operator Safety Wears
- Optional Equipment
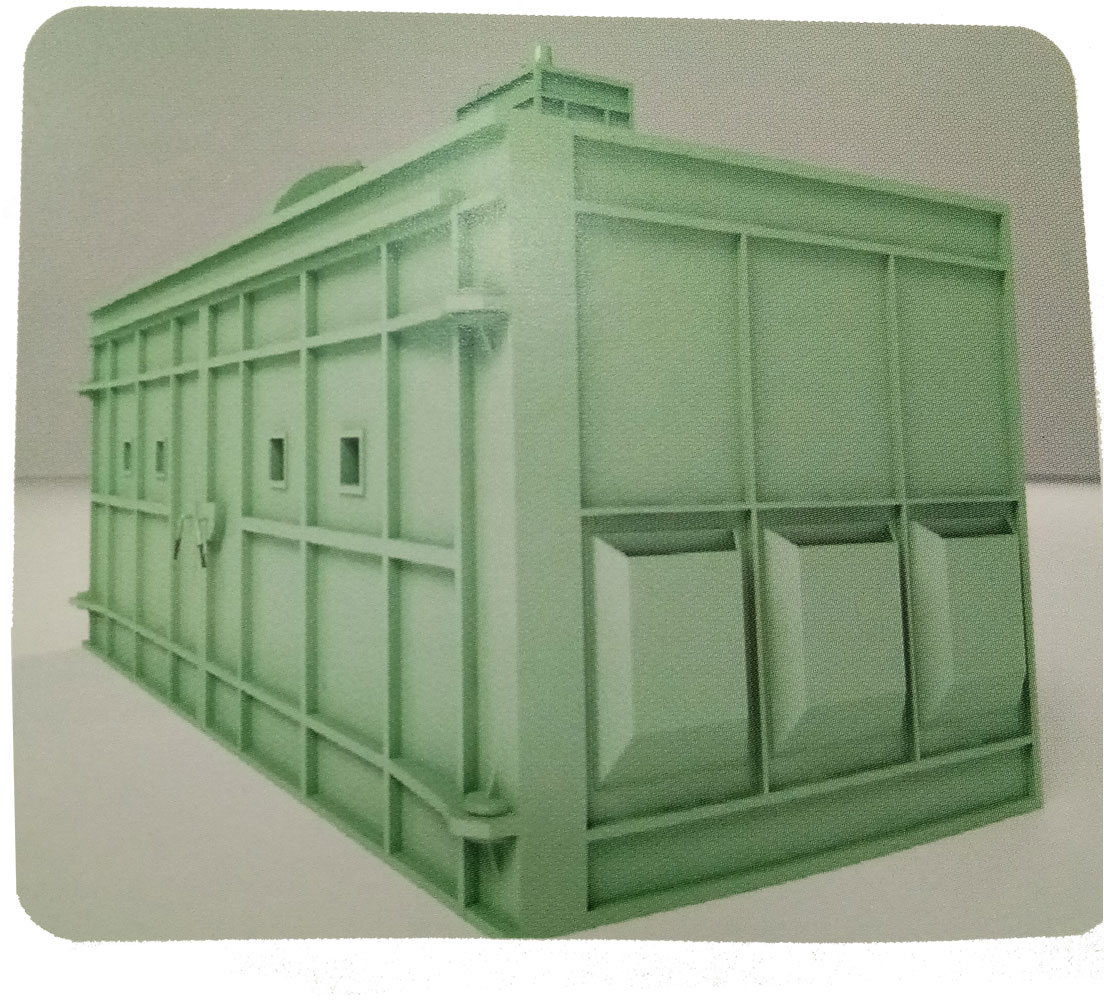
Enclosure
The modular blast room is specially ventilated and illuminated for enclosed abrasive blasting and is a fully sealed, dust-tight, all-steel structure. The components are prefabricated for simple bolt-together erection, with little or no job site welding required. The ENCLOSURE stands by its own structural support without connections to the surrounding facilities. The size of the enclosure depends on
- The size of the job
- Number of operators
- Adequate working space around the job
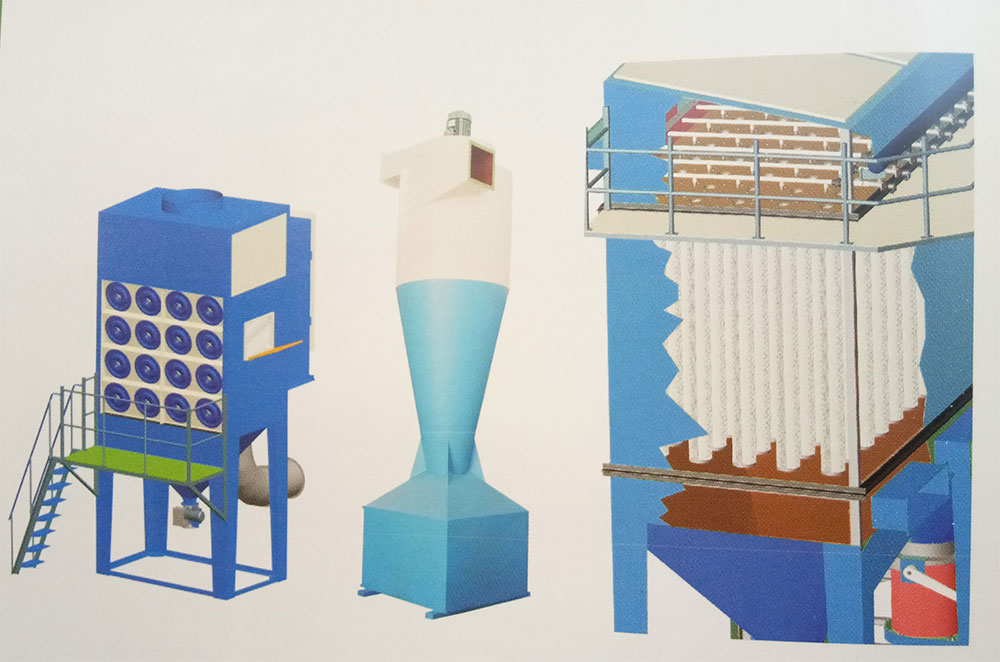
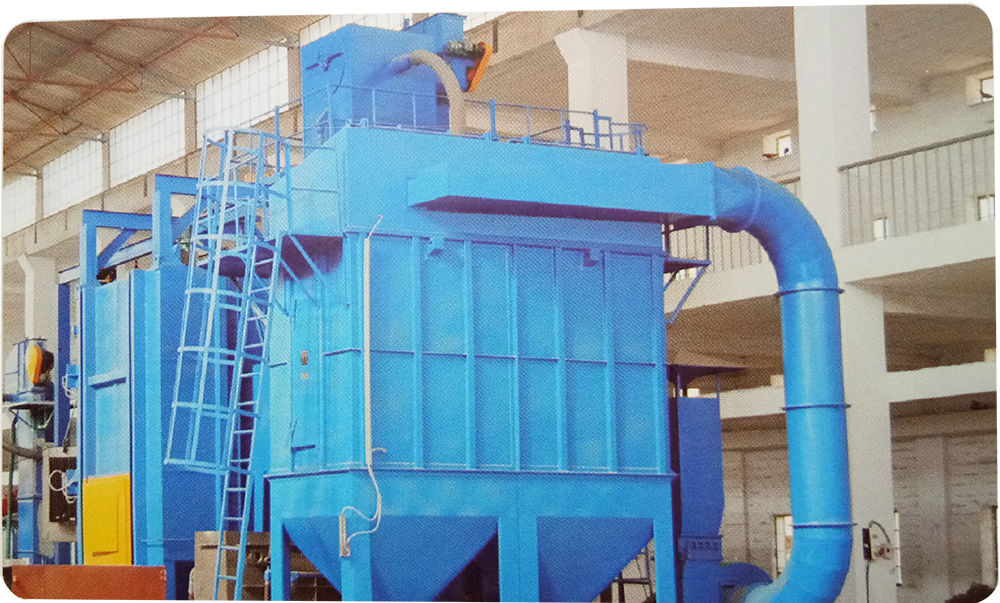
It also influences the size of the dust collector and reclaimer installation costs.
Dust Collector / Extractor Unit
The choice of the correct model of dust collector is integral to any closed environment blasting system. It is essential to remove dust and fine abrasive particles from the environment of the blast chamber to maintain efficient operation.
The Dust collectors are broadly classified into four types
- Cyclone Type
- Fabric Bag Type
- Cartridge Filter Type
- Pleated Bag Type
In operation, the exhauster fan on the clean air side of the collector draws dust-laden air from the blast room through the fabular filter bags. Dust collects on the inner side of the bags, and when the exhaust fan is turned off, the bag shaker mechanism reconditions the filters by shaking most of the caked dust from inside of the bags into a dust-collecting hopper.
Blasting Media Recovery & Separation System
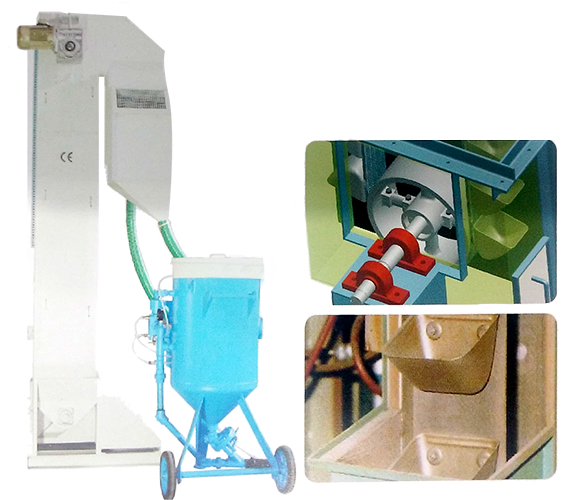
Bucket Elevator
The buckets are of the seamless type made of a 3.15mm thick steel sheet. The bucket elevator is fabricated from Ms material 5mm thick at the boot section and 3.15mm thick at the trunk and top section, respectively. A one-piece cast iron pulley, which has been crowned for tracking & rubber lagged to prevent slippage, is located in the boot & head section of the elevator to drive the belt.
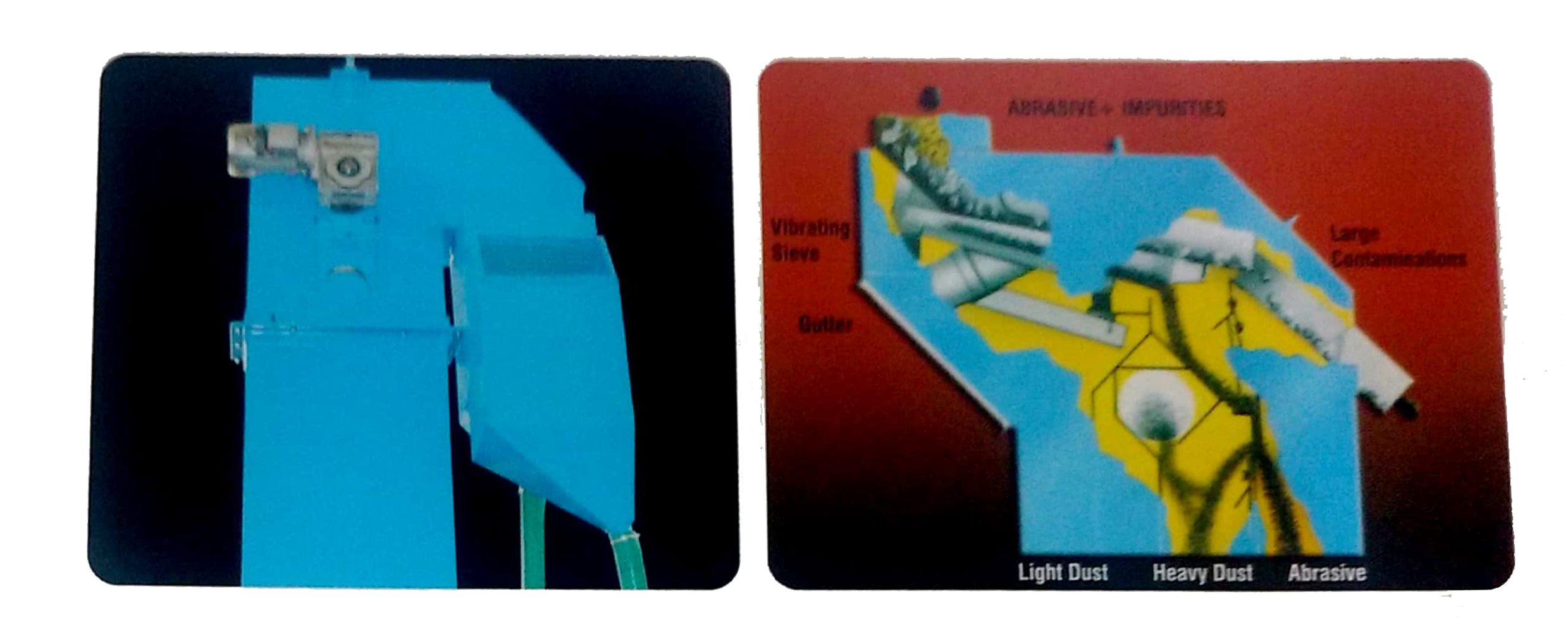
The media separation unit is in an air wash rotary screen separator, which receives all media and debris from the blasted workpiece by the bucket elevator. Contaminants are removed by rotary screen & are discharged through a chute. The finer contaminants are abrasive that pass through the screen and then cascade over the air wash, where fine contaminants and small abrasive particles are removed. Reusable abrasive falls in the machine.
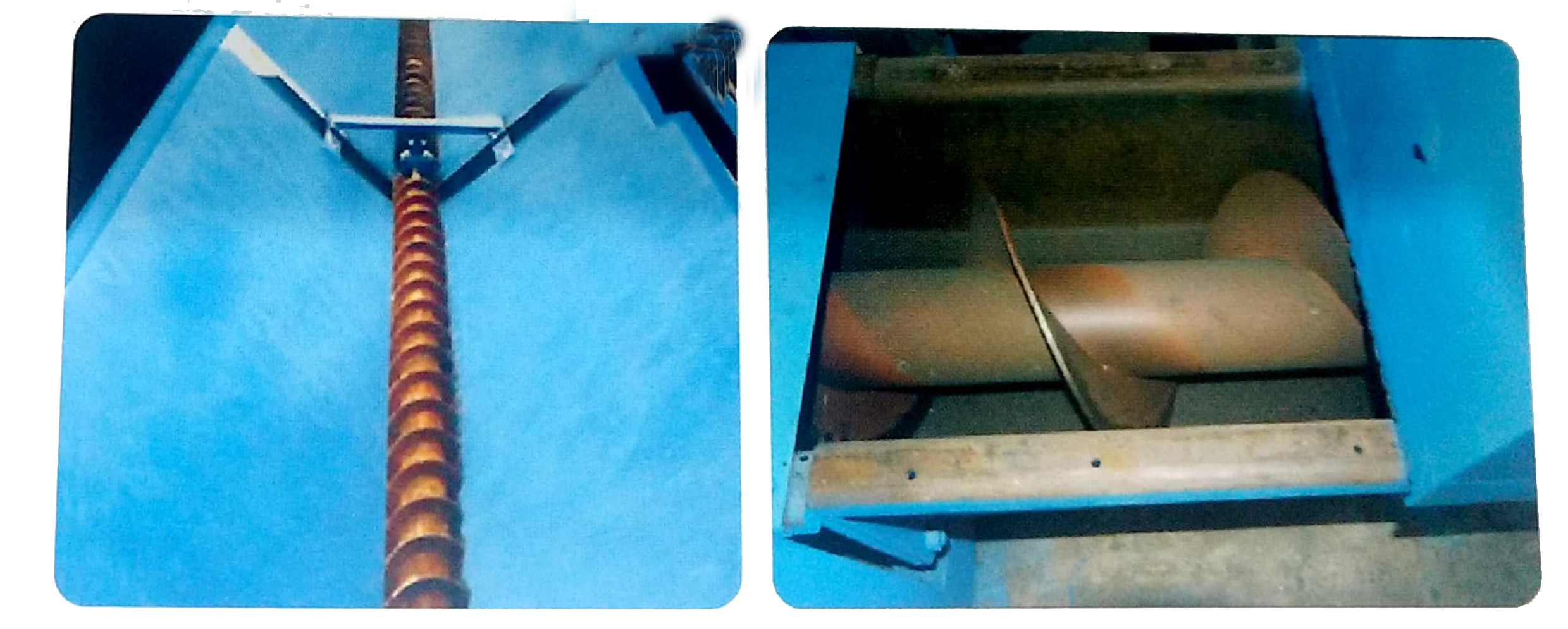
The reclaim floors utilize a heavy-duty screw to return the abrasive to the separator/classification system. The standard screw is 9” in diameter, which consists of a 5” diameter schedule - 40 pipe wrapped with ¼” thick flighting.
Floor Design
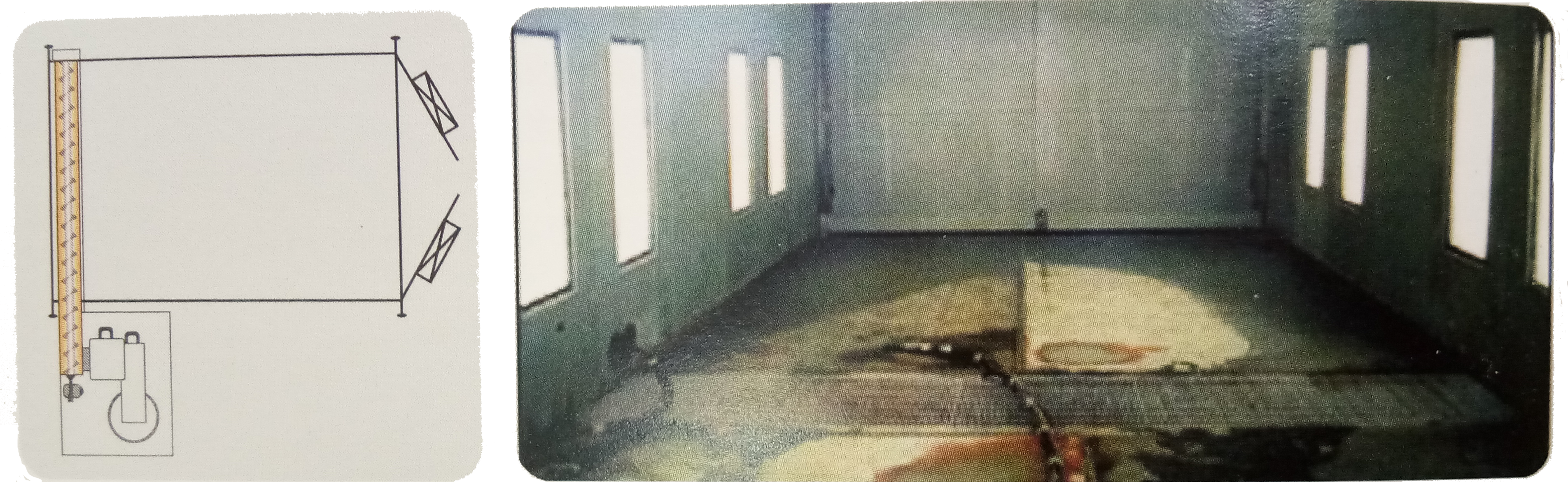
A single-screw partial reclaim system is the most economical floor design available. The system contains the major components heavy-duty screw, belt, bucket elevator, air-wash separator, perforated plate rotary drum separator, and oversized abrasive storage hopper with a caged man ladder and handrail. This is a basic “automatic” reclaim package that can be expanded to an “H,” “U,” or full floor reclaim system. It is best suited for low to medium production levels.
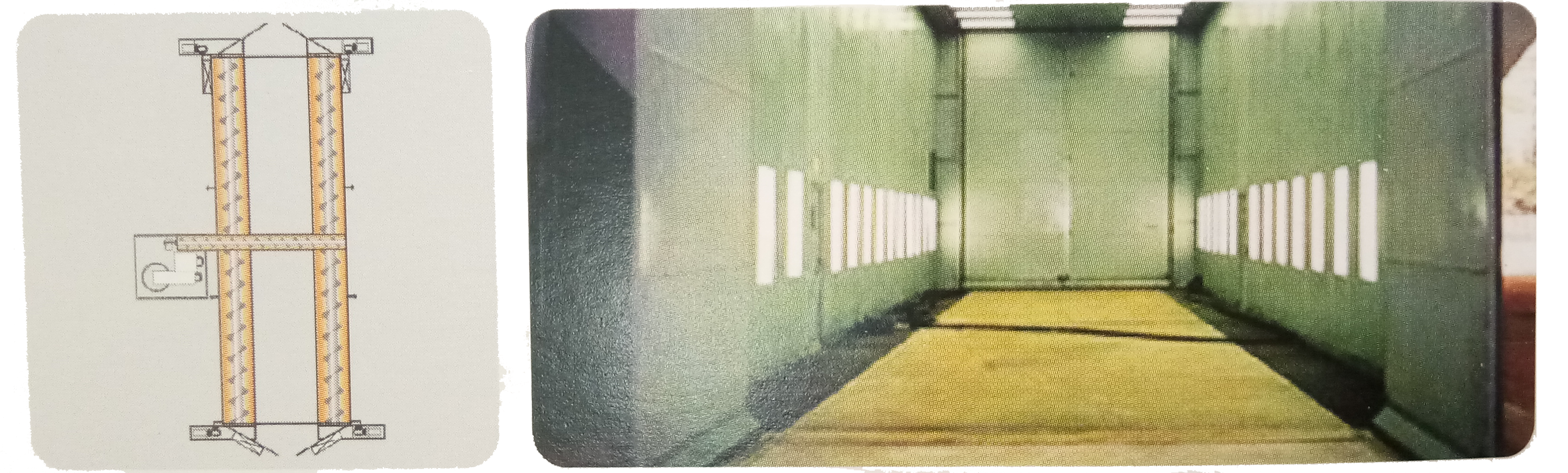
The “H” shaped partial reclaim system adds two longitudinal screw assemblies along each side wall of the blast room. The position of the screw assemblies allows the abrasive delivered from the blasting nozzle, which is either blown or rebounded off the work piece, to strike the side walls and fall into the screws, automatically reclaiming approx. 60 - 90% of the blast media. This system is best suited for medium to high production.
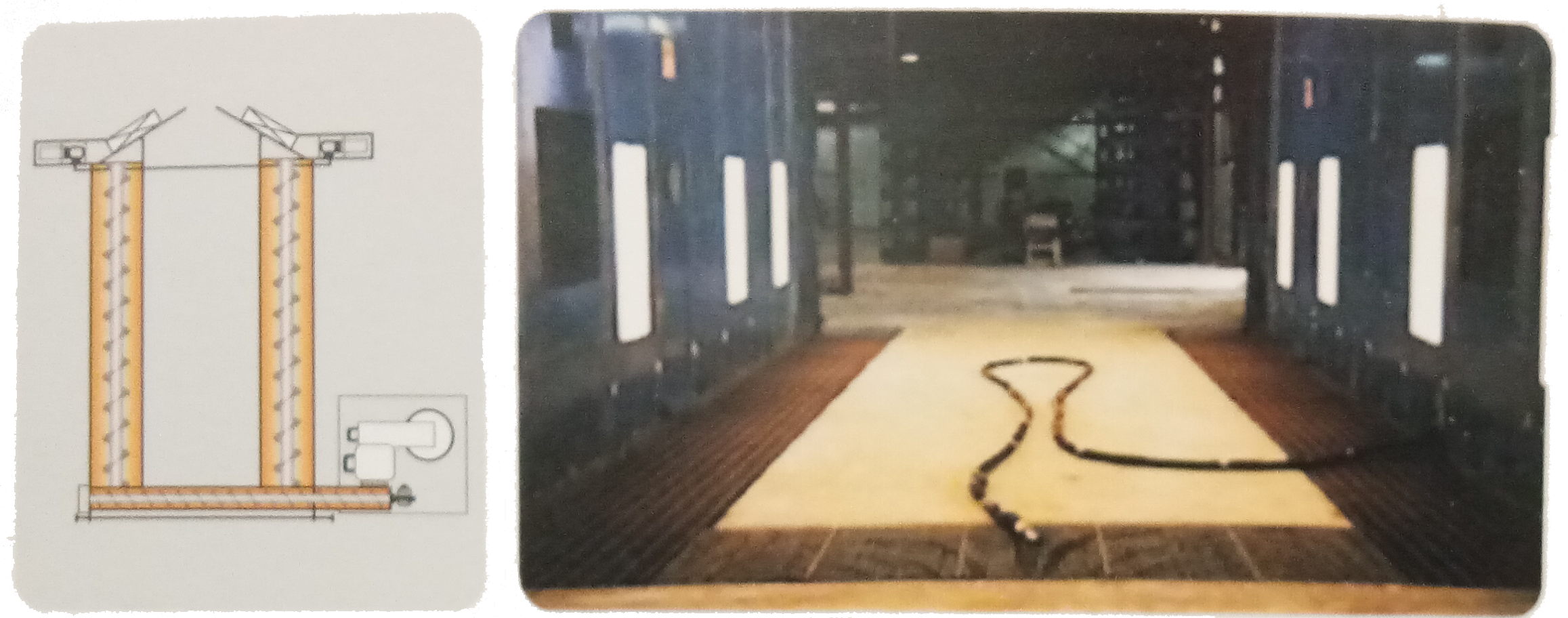
The “U” shaped partial reclaim system adds two longitudinal metered screw assemblies along each side wall of the blast room. The position of the screw assemblies allows the automatic reclaiming of approx. 60 - 90% of the blast media. This floor design is typically utilized in a “flow-through” room configuration where heavy work pieces and/or material handling devices can drive into the room and position the workpiece on the steel-covered concrete floor located between the longitudinal screws. This system is best suited for medium to high production.
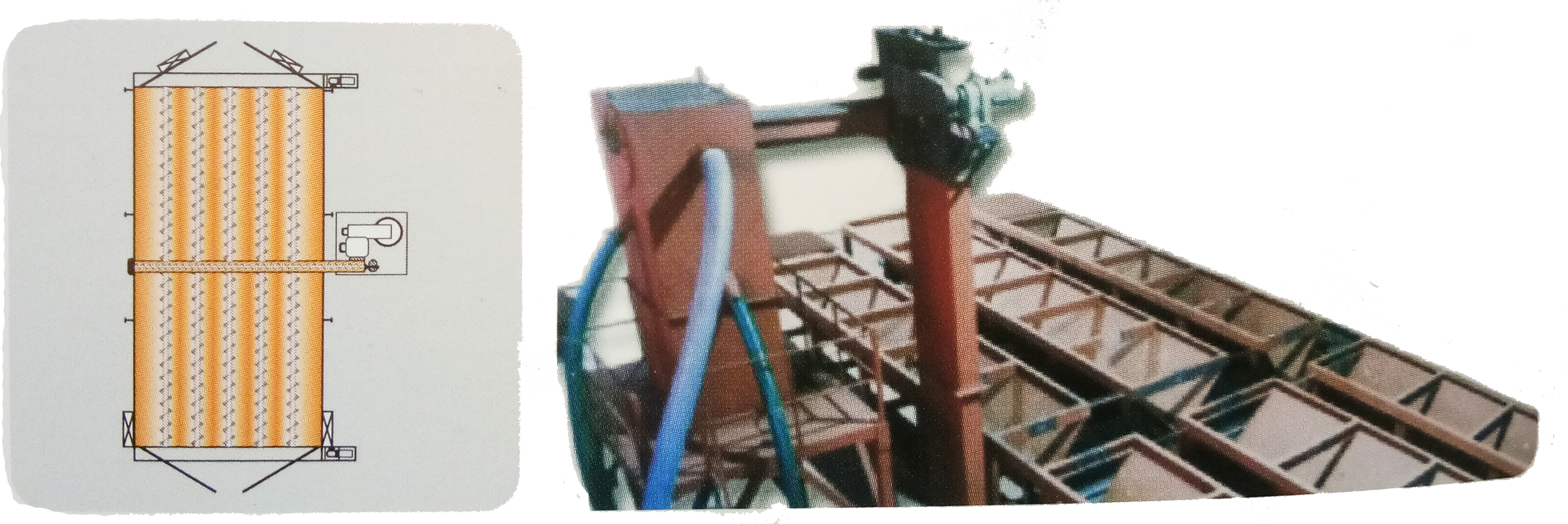
The full floor reclaim system utilizes multiple screw assemblies to create a fully automatic abrasive reclaim system, where 100% of the blast media is required to the separator system during the blasting operation. This system is best suited for high production requirements.