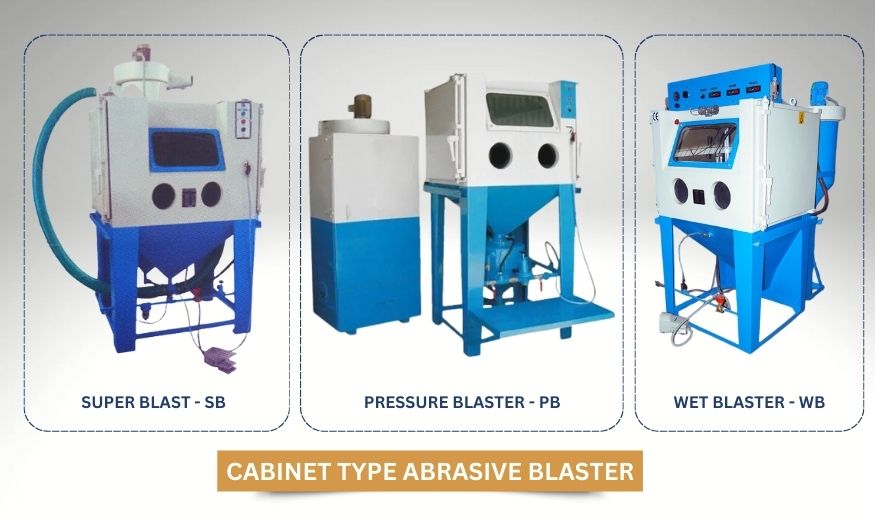
Process & System is a renowned manufacturer and supplier of cabinet-type abrasive blasters, designed to provide precise and efficient solutions for a wide range of surface preparation, cleaning, and finishing tasks. Our state-of-the-art abrasive blasting machines are developed with advanced technology to cater to various industrial needs, including light to heavy-duty applications.
We offer three distinct types of cabinet-type abrasive blasters: Super Blast (SB), Pressure Blaster (PB), and Wet Blaster (WB), each uniquely designed to meet specific surface treatment requirements. Whether you’re a manufacturer in the automotive industry or a tool and die maker, our machines are engineered for reliability, performance, and durability.
Super Blast (SB) – Induction/Suction Blaster
As a leading supplier of Super Blast (SB) machines, Process & System offers an advanced abrasive blaster that operates on the Induction-Suction principle. This model is ideal for industries that require continuous, uninterrupted blasting cycles with precision and consistency. Apart from this we also manufacture airless shot blasting machine, tumblast shot blasting machine, etc.
Working Principle of SB Cabinet Abrasive Blaster
The Super Blast uses the Induction-Suction principle for abrasive delivery, ensuring continuous operation without downtime. The abrasive material is drawn into the system using suction and propelled at high speed for surface treatment.
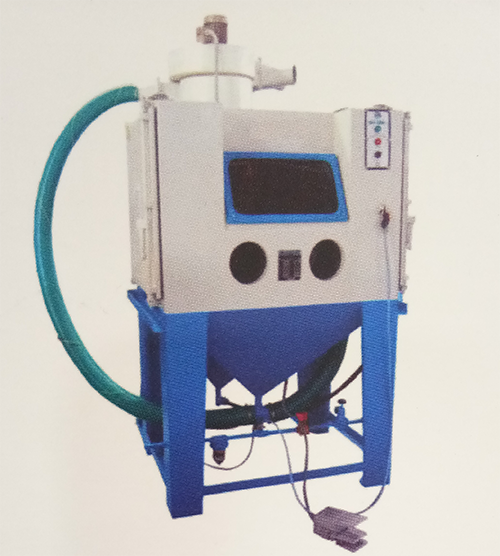
Applications of SB Cabinet Abrasive Blaster
These are the main applications that this machine gives.
- Designed for light and medium-sized components, the SB is perfect for tasks like surface cleaning, deburring, and imparting a fine matte finish.
- It is particularly useful in heat treatment shops, tool rooms, and for die and mold makers. Additionally, the Super Blast is highly effective for shot peening of light metal components, enhancing surface durability and stress resistance.
Features of SB Cabinet Abrasive Blaster:
The primary features of this machine are:
- Reclaimer System: A standout feature of our SB machines is the integrated reclaimer, which automatically cleans and separates the abrasive. This ensures that only clean and properly sized abrasive particles are used in the blasting process, resulting in a homogeneous and consistent finish across all operations.
- Dust Management: The system effectively separates dust and debris from the abrasive, minimizing contamination and enhancing operational efficiency.
Advantages of SB Cabinet Abrasive Blaster:
The main advantages include:
- Continuous Operation: With no interruption during the blasting cycle, you can achieve greater productivity.
- Precise Finishing: The clean and uniform abrasive ensures a high-quality matte finish, ideal for industries that demand precision.
- Low Maintenance: The automatic abrasive cleaning reduces maintenance efforts, saving both time and operational costs.
Pressure Blaster (PB) – Direct Pressure Blaster
At Process & System, we are well-regarded manufacturers and suppliers of the Pressure Blaster (PB), which operates on the Direct Pressure principle. This powerful blaster is designed for high-velocity abrasive delivery, making it ideal for faster, more aggressive cleaning operations.
Working Principleof PB Cabinet Abrasive Blaster
The Pressure Blaster relies on the Direct Pressure principle, where abrasive is delivered at high speed, resulting in quicker and more efficient cleaning of surfaces. This method is best for heavy-duty applications that require removal of tough surface contaminants.
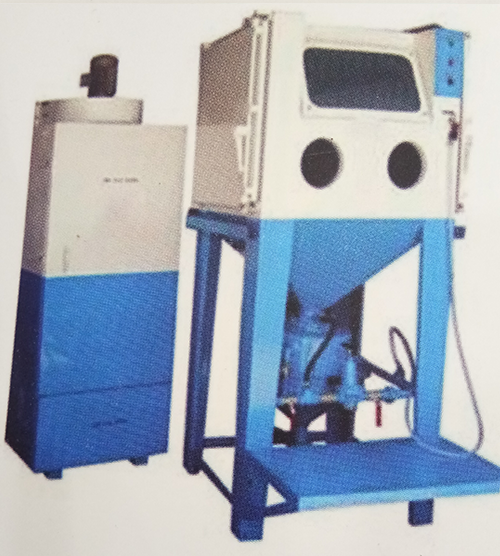
Applications of PB Cabinet Abrasive Blaster:
The main applications of this machine includes:
- The PB is especially suited for removing heavy rust, corrosion, and preparing surfaces for subsequent treatments such as rubber lining, FRP lining, and metal spraying.
- It is also ideal for cleaning castings and forgings, where rapid surface preparation is required.
- The machine’s versatility makes it suitable for manufacturers in industries such as metal fabrication, automotive, and aerospace.
Features of PB Cabinet Abrasive Blaster:
The primary features are:
- High Velocity Blasting: The high abrasive velocity allows for fast removal of surface contaminants, enabling faster job completion and increased throughput.
- Automatic Abrasive Refilling: The pressure vessel is bolted directly below the hopper and features an automatic abrasive refilling system, ensuring continuous operation without manual intervention.
- Dust Collection System: The tubular fabric bag-type dust collector ensures high dust collection efficiency. The manual shaker provided helps to clean the dust filter, ensuring the system operates at peak efficiency.
- Adjustable Pressure: The blast pressure can be easily controlled from 30 to 90 psi, allowing operators to adjust the system based on the specific application or abrasive material.
Advantages of PB Cabinet Abrasive Blaster:
The primary advantages include:
- Speed and Efficiency: Designed for fast surface cleaning and preparation, the PB can significantly reduce operational time, particularly in industries with high throughput demands.
- Heavy-Duty Performance: Suitable for coarse and medium-sized abrasives, the PB can handle tough jobs where heavy rust or large contaminants need to be removed quickly and effectively.
- Cost-Effective: The fast processing and automatic refilling system reduce labor costs and downtime, improving overall efficiency.
Wet Blaster (WB) – Induction/Suction Wet Blasting
Process & System also supplies the Wet Blaster (WB), a specialized abrasive blaster designed for precision surface treatment using the Induction-Suction principle in conjunction with liquid suspension. This model is highly effective for delicate applications where fine abrasive is required.
Working Principle of WB Cabinet Abrasive Blaster:
The Wet Blaster works by suspending fine abrasive particles (as small as 5 microns) in a liquid, typically water. This slurry is then pumped to the nozzle, where it is introduced into an air stream and propelled onto the workpiece. This method results in gentle yet effective surface treatment, making it ideal for precision components.
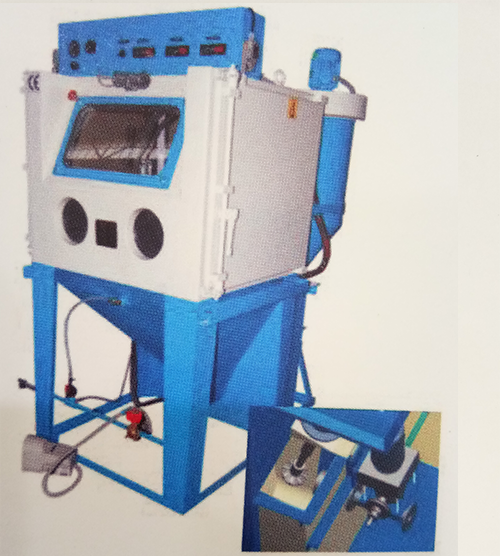
Applications of WB Cabinet Abrasive Blaster:
The primary applications are:
- The WB is perfect for tasks that require super-finished surfaces, such as deburring multi-tooth cutting tools (e.g., milling cutters, broaches, and taps) and removing feather burrs.
- It is also useful for deburring intersecting holes in precision parts, providing a highly precise finish that is not achievable with other methods.
- Industries like medical device manufacturing, tool and die making, and aerospace benefit greatly from the WB’s ability to finish surfaces without damaging sharp edges or compromising tolerances.
Features of WB Cabinet Abrasive Blaster:
The main features include:
- Fine Abrasive Usage: The Wet Blaster can use extremely fine abrasive particles, allowing for a more detailed and delicate finish.
- Glandless Slurry Pump: The slurry pump is made from thermoset plastic materials for superior corrosion resistance and durability, ensuring longevity and reduced maintenance.
- High Precision Finishing: The WB can deburr and finish the most delicate and complex surfaces without any damage, making it ideal for industries where precision is key.
Advantages of WB Cabinet Abrasive Blaster:
There are numerous advantages of getting such machines from the top supplier in Kolkata, India.
- Superior Surface Finish: The wet blasting method provides a smooth, polished finish, especially suitable for sensitive or complex parts.
- Time-Saving: Eliminates the need for hand-finishing processes, significantly reducing labor costs and production time.
- Environmentally Friendly: The wet blasting method generates less dust, providing a cleaner and safer work environment.
Technical Specification:
Model | Pressure Blaster(PB) | Super Blaster(SB) | Wet Blaster(WB) | |||||
---|---|---|---|---|---|---|---|---|
PB - 9182 | PB - 12090 | PB - 150120 | SB - 6060 | SB - 9182 | SB - 12090 | WB - 9182 | WB - 12090 | |
Working Chamber (mm) Height Weight Depth |
775 910 820 |
900 1200 900 |
900 1500 1200 |
600 600 600 |
775 910 820 |
900 1200 900 |
775 900 820 |
900 1200 900 |
Door Opening (mm) Weight Height |
730 675 |
800 800 |
1100 800 |
500 500 |
730 675 |
800 800 |
730 675 |
800 800 |
Overall Dimension (mm) Height Weight Depth |
2130 1100 2500 |
2030 1365 2430 |
2080 1665 2730 |
1660 800 1500 |
2120 1070 1400 |
2570 1365 1700 |
1940 1070 1500 |
2235 1365 1700 |
Dust or Mist Collector or Reclaimer Fan Motor HP Fan Capacity (M3/min) Fan Capacity (CFM) Filter Cloth Area (M2) Slurry Pump Motor (HP) Airjet Orifice (mm) Blast Nozzle (mm) |
1.0 14.16 500 7.5 --- --- *5,6 |
1.0 14.16 500 7.5 --- --- *5,6 |
1.5 22.66 500 7.5 --- --- *5,6 |
0.5 5.66 200 1.0 --- *2,3 *6,8 |
1.0 11.32 400 2.0 --- *3,4,5.5 *8,10,12 |
1.5 16.98 600 4.0 --- 3,*4,5.5 8,*10,12 |
0.5 5.66 200 --- 1.0 *3,4,5.5 *8,10,12 |
1.0 11.32 400 --- 1.0 *3,4,5.5 *8,10,12 |
Abrasive Storage Capacity Litres (CFT) Pit Size (mm) Weight Length Depth Weight in Kg (approx.) |
28 (1.0) --- *5,6 |
42 (1.5) 600 2180 510 650 |
42 (1.5) 900 2530 600 760 |
28 (1.0) --- 250 |
28 (1.0) --- 380 |
42 (1.5) --- 490 |
42 (1.5) --- 400 |
42 (1.5) --- 525 |
Abrasive Feed | Direct Pressure | Induction Suction | Glanless Pump |
Cost of cabinet-type abrasive blasters
Our cabinet-type abrasive blasters are competitively priced, starting from ₹55,000 and ranging up to ₹2.5 lakh, depending on the specific model and spare parts. We offer scalable solutions for businesses of all sizes, from small workshops to large manufacturing plants.
Industries Served
Process & System caters to a broad range of industries, including:
- Automotive: Surface preparation and cleaning for automotive parts.
- Aerospace: Precision surface treatment for aircraft components.
- Manufacturing: Deburring and cleaning of castings, forgings, and machined parts.
- Tool and Die Making: Precision finishing for tools, dies, and molds.
- Heat Treatment: Shot peening and cleaning for heat-treated components.